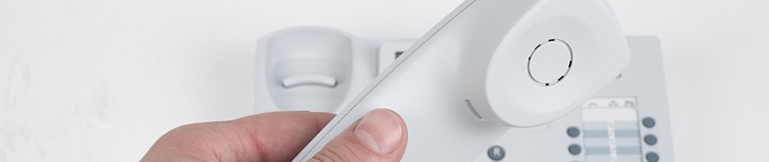
- Home > Auxiliary column >
News
NEWS
BMW's Carbon Core and more
Release date: BMW's Carbon Core and more
In this feauture for Plastics News EuropeDavid Vink reports from IAA 2015, which showed BMW and other OEMs adopting a multi-material approach to lightweighting.
BMW uses carbon fibre reinforced plastic (CFRP) in its new 7-series car which was launched at the IAA 2015 automotive fair in Frankfurt. BMW has given the name Carbon Core to the multi-material structure in aluminium, high strength steel and CFRP, which contributes towards 133 kg weight-saving over the preceding 7-series car. The company says the new 7-series is the first within its traditional model portfolio using industrially produced CFRP in its body structure, rather than as a visible exterior body skin, profiting significantly from the group’s CFRP experience in the i-series electric cars.
The 22 CFRP parts are produced at BMW’s lightweight competence centre in Dingolfing on five Dieffenbacher wet compression moulding and two hybrid pressing lines featuring Compress Lite presses. Aside from roof frame crossbeams, they provide additional reinforcement of B- and C-pillars, door sills, the central tunnel and baggage area separation wall. The lines include equipment from Frimo and KraussMaffei.
Two curved round hollow CFRP profiles applied lengthwise along the roof frame are produced in Landshut. They were originally conceived for production by braiding carbon fibre over a solid foam plastic core, followed by epoxide (EP) resin impregnation and curing during pressing in the high-pressure resin transfer process (HP-RTM). But BMW switched at a late stage to a hollow plastic profile that is prevented from collapse during compression moulding by heated demineralised water under pressure, produced with equipment designed and supplied by water assist equipment producer Maximator.
BMW says wet moulding in Dingolfing replaced HP-RTM of dry preforms (with resin injected in a closed mould) as still used in other BMW plants. It involves compression moulding EP resin‑impregnated carbon fibre fabric in wet state into final pressed and cured 3D parts. Hybrid pressing is wet moulding with wet impregnated fabric pressed and cured together with sheet steel, bonding it to steel in the final hybrid part. BMW praises wet processes as enabling economic large-series production in compact equipment, with short cycle times allowing production of up to several thousand parts per day.
Dieffenbacher says the CF core layers or “stacks” are ultrasonically welded prior to robotic resin application while other parts cure in the press at 150°C. This saves time in the fully automated process, equipped with a Kuka articulated arm robot, as does simultaneously multiple part moulding.
At IAA 2015, Porsche presented its 500km range, e-mission 4-seat sports car concept study with doors opening in two directions. The company predicted it would launch the car “at the end of the decade”, pointing to a “functional mixture of aluminium, steel and CFRP”, with carbon intended for wheels.
Automotive supplier Magna showed a CFRP car hood, made by compression moulding EP resin pre-impregnated preforms (prepregs), with overall 10 min cycle time including 8 min cure, composites global product line director Andrew Swikoski told Plastics News Europe. He revealed the hood is produced for Cadillac ATS-V coupe and CTS-V sedan cars. It weighs 25-30% less than aluminium hoods, while providing increased stiffness and improved aerodynamics.
The Ford Mustang front-end carrier (or bolster) displayed by Magna at IAA consists of upper and lower injection moulded 20% CF reinforced PA6 parts welded together by electric resistive implant welding (RIW) via stainless steel inserts into a high stiffness closed box structure. Swikoski told Plastics News Europe stainless steel use prevents CF “kicking off corrosion” as in normal steel. There is 25-30% weight saving over conventional composite/metal hybrid bolsters, Magna claims.
Kirchhoff Automotive presented at IAA a prototype of a front-end in a multi-material mix of organic sheet, steel and glass mat thermoplastic (GMT) with 50% weight saved. It chose glass fibre based solutions due to relatively low GF cost compared with CF.
CF cost is also of concern for door module producer Brose. The company saves weight with extensive use of GF-based organic sheet in seat structures and door modules and has recently started up a new organic pre-fabrication unit, but CEO Jürgen Otto told Plastics News Europe that CF is still too expensive.
Brose says 0.5mm thick organic sheet saves 5 kg per vehicle versus steel door modules and absorbs four times as much energy, on account of its layered structure and local reinforcement, yet functional elements, such as window regulator rails, can still be integrated into the organic sheet. Combined with other materials, organic sheet contributes to Brose’s claim that the front-seat structure is the “lightest solution in the market”, weighing 20% less than comparable front seat structures. The seat structure weighs 15 kg and the back panel is in “a combination of paper and plastic”. Organic sheet in the second-row load-through saves up to 1.5 kg/vehicle over sheet steel.
Mubea Muhr & Bender showed a B-column in a hybrid steel tailored rolled blanks (TRB) and fibre reinforced plastic (FRP) solution developed with consultants EDAG. While today’s all‑steel B-columns weigh 7.7 to 9.5 kg, the Hybrid TRB/FRP solution weighs 6.2 kg.
The single-layer Mubea GFRP Tension leaf spring saves up to 60% weight over steel springs, and an integral CFRP underbody offers low weight with a high degree of functional integration. A CFRP roof design also saves 7 kg weight. Although not mentioned by Mubea, a visible CFRP roof has been developed by the AZL automotive lightweight centre at RWTH university for the Opel Astra OPC Extreme sports car. As a study for low-volume production runs, the 1.5 kg roof was displayed by Opel and AZL in 2014 at the RWTH IKV colloquium and the Geneva Auto Show.
Pride of place on the Mubea IAA stand went to a Mubea Performance Wheel Hybrid, claimed as a world-first application of CFRP in hybrid wheels that was “soon to go into series production on a premium class car”. It enables 10 kg per car weight-saving compared with forged aluminium wheels.
Maxion Wheels, claiming to be the world’s largest steel and aluminium wheel manufacturer, showed a hybrid wheel saving up to 40% weight over an all‑aluminium wheel. This hybrid wheel was made with a CFRP rim and a liquid‑forged aluminium disc. Maxion developed it for the luxury and sports car segment together with ThyssenKrupp Carbon Components with “unique braiding technology” under a co-operation agreement concluded in June 2015. Such hybrid wheels also form part of ThyssenKrupp’s InCar Plus lightweighting programme and Maxion said Volkswagen had already started testing the wheels on vehicles.
Webasto chairman Dr Holger Engelmann spoke about polycarbonate glazing, which has so far been limited to roofing and fixed rear side windows, but has potential to substitute glass in front windows and even the windscreen. “We are of the opinion it is now the time to give greater importance to this technology. With its properties, PC has the potential to replace glass in all glazing”, he said.
The company promotes this all-round approach in its Polycarbonate 360 programme together with an OEM partner.
Despite international expansion, Engelmann confirmed to Plastics News Europe that polycarbonate glazing is still produced only at Webasto’s Schierling facility. Webasto staff referred Plastics News Europe to five moulding machines: a 3,200 tonne Engel Duo, plus three KraussMaffei and one Engel machine with 2,300 tonnes clamping force, used for two-component PC roof glazing.
In addition to the new Smart ForTwo polycarbonate roof, Webasto showed opaque PU composite spray moulded (PU-CSM) roofs (see pages 14-15). The structured surface film-clad roofs are made for new Smart and Jeep Renegade cars, in respectively fixed and removable versions.
Webasto staff told Plastics News Europe the new type PU-CSM roofs are much lighter than long glass fibre injection (LFI) ones (as earlier for the Smart), due to use of a paper honeycomb (PHC) core combined with the glass fibre reinforcement. The Renegade one weighs 50% less than a glass equivalent. A red painted high gloss Class A surface roof made with the PU-CSM PHC core was shown: it was produced with a thin 0.5mm aluminium layer under the paint and weighed around 4.5 kg per square metre.